The rendering mix ratio for external and internal walls can vary depending on factors such as the type of wall surface, climate conditions, and the desired finish. However, here is a general guideline for common rendering mix ratios:
1. External Walls:For a base coat (scratch coat), a common mix ratio is 1 part cement to 4 or 5 parts sand and for a topcoat (finishing coat), you can use a mix ratio of 1 part cement to 3 parts sand.
2. Internal Walls:Internal walls may require a finer finish, so a common mix ratio is 1 part cement to 2 or 3 parts sand for the base coat and for the finishing coat on internal walls, a mix ratio of 1 part cement to 1.5 to 2 parts sand is often used.
Rendering is the process of applying of lime cement mortar to external, internal or partition brick/ block walls to achieve highly finished, good texture and smooth surface, which give us aesthetic and beautiful appearances, it should be waterproofing and fire rating qualities.
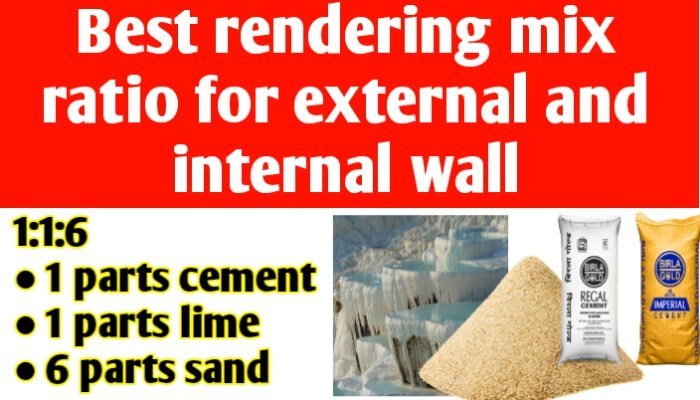
Its other name is plastering, very much common and used in European countries particularly around mediterranean like Albania, Algeria, Bosnia and Herzegovina, Croatia, Cyprus, Egypt, France, Greece, Israel, Italy, Lebanon, Libya, Malta, Monaco, Montenegro, Morocco, Slovenia, Spain, Syria, Tunisia, and Turkey.
Most renders are typically consist of sand, cement, lime and water. A standard render mix ratio is 6:1:1 for external and internal walls. In creating 6:1:1 mix, 6 parts sand mixed with 1 part cement and 1 part lime.
Best mix ratio for rendering
The main ingredients of renders are Portland cement, sand, lime, water and some approved admixture, normal, commonly used, standard and most suitable.
Recommended best mix ratio for rendering is 6:1:1 for external and internal walls. In a 6:1:1 render mix ratio, 6 parts of sand mixed to 1 part cement to 1 part of lime by volume. The numbers indicate the parts of each material based on volumetric analysis.
The optimal mixing ratio for rendering is 6:1:1 for exterior and interior walls. Mix 6 parts sand with 1 part cement and 1 part lime in a render mix ratio of 6:1:1. The numbers indicate the parts of each material based on volumetric analysis.
Render mix ratio: The optimal render mix ratio for rendering is 6:1:1 for exterior and interior walls. Mix 6 parts sand with 1 part cement and 1 part lime in a 6:1:1 ratio. Typical renders consist of sand, cement, lime and water.
Any general purpose cement can be used and sand must be fine rendering sand clean and free from impurities. You do not use building sand for rendering because it may causes shrinks and cracks.
Renders is mix with some additives material that increases the bonding strength and slowing in drying or hardening, adding lime in mix increases the plasticity, flexibility and workability that can reduces the chance of cracking after drying. Pigmentation of colour should be done according to aesthetic requirement. A thin finishing top coat can be applied to achieve decorative effect, it can be applied by using trowel, brush or sponge.
Rendering mix ratio for external and internal wall
Typically, most of renders are made of Portland cement, sand, water, lime and some approved additive ingredients.
The standard rendering mix ratio for external and internal walls is 6:1:1 which indicates 6 parts of sand to 1 part cement to 1 part hydrated lime by volume. For this mix, any general purpose cement can be used and sand should be fine and clean of impurities, coarser sand is usually used for base layer and finer sand for the top layer.
How thick should render be?
A typical render should be 20mm thick for external walls and 12mm thick for internal walls. The typical thickness of render for external walls must be 10mm, 12mm or 15mm for first coat and 5mm, 6mm or 8mm thick for finished second top coat. This never be exceed from 20mm. Thickness of render for internal wall must be 1 coat of 10mm, 12mm or 15mm thick, if 2 coats is applying, then first coat should be 10mm thick and second top coat should be 5mm thick.
Minimum and maximum thickness of render
The minimum render thickness on interior walls must be 10 mm and a maximum of 20 mm on exterior walls.
Thickness of render depending on types of application, external and internal wall, plane or rough face, minimum thickness of render should be lying between 10mm, 12mm to 15mm and maximum thickness of render should be do not exceed from 20 mm, either contain 1 coat or 2 coat.
◆You Can Follow me on Facebook and
Subscribe our Youtube Channel
Best cement for rendering
The best cement for rendering is Ordinary Portland Cement of grade 43. Any general purpose cement can be used for rendering, that should be either made from Portland stone, dust, slug or fly ash. Ordinary Portland cement of grade 43 looking as best to use for rendering, pozzolanic Portland cement (PPC) also looking good but it can causes fast setting and Portland slag cement used especially in marine area. So do not confuse with best cement for rendering, looking over the market, which is available, select the best cement as per your choice and requirement.
Best sand for rendering
The sand for rendering must be plastering or rendering sand. It should be clean, fine texture and free from any organic impurities. You do not use building sand for rendering because it may causes shrinks and cracks. You can use some amount of building sand as base coat, but it does not seems like that it is primarily sand for rendering.
Conclusions:-
The optimal rendering mix ratio is 6:1:1 for exterior and interior walls. Mix 6 parts sand with 1 part cement and 1 part lime in a render mix ratio of 6:1:1.